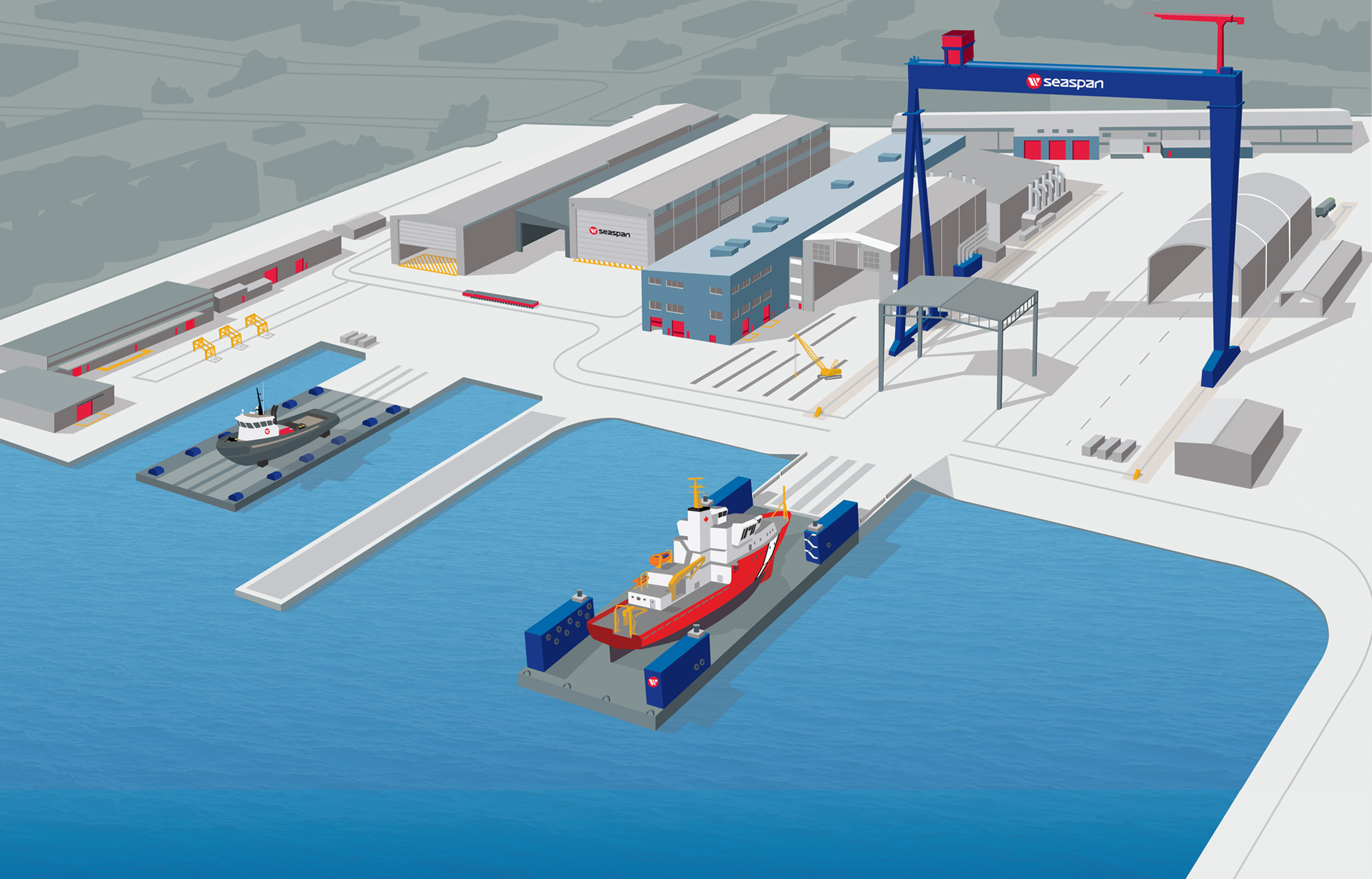

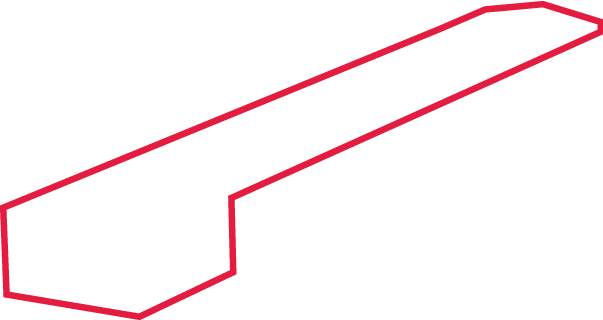
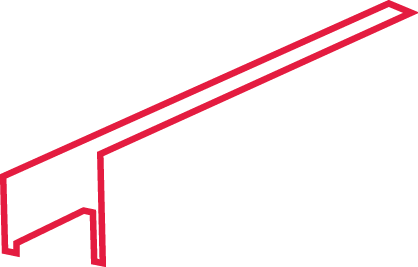
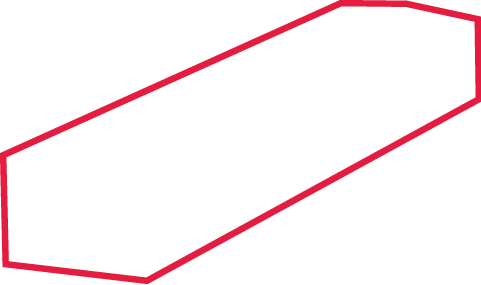
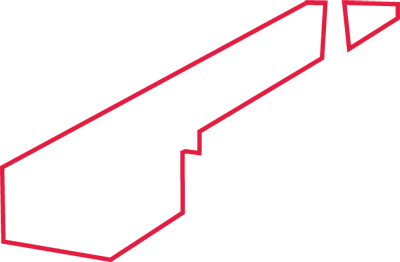
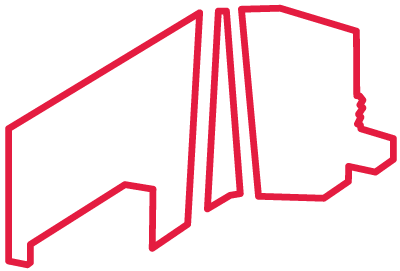
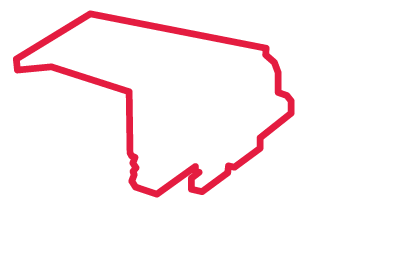
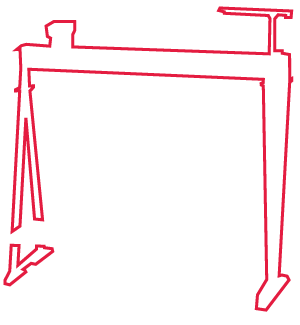
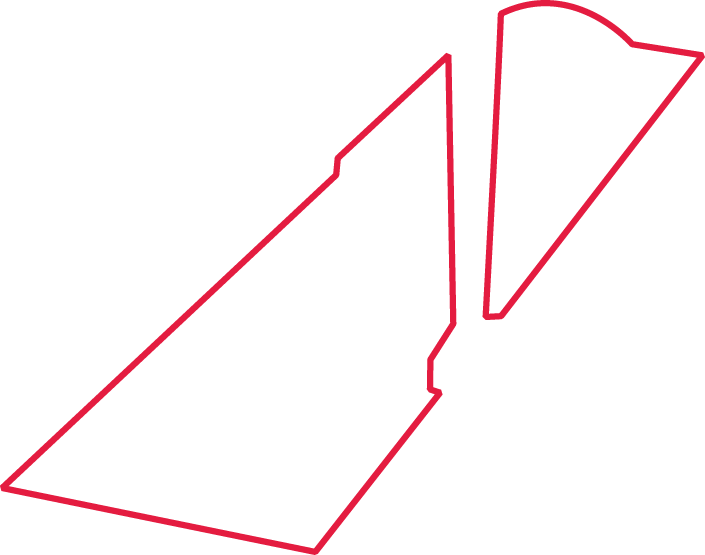
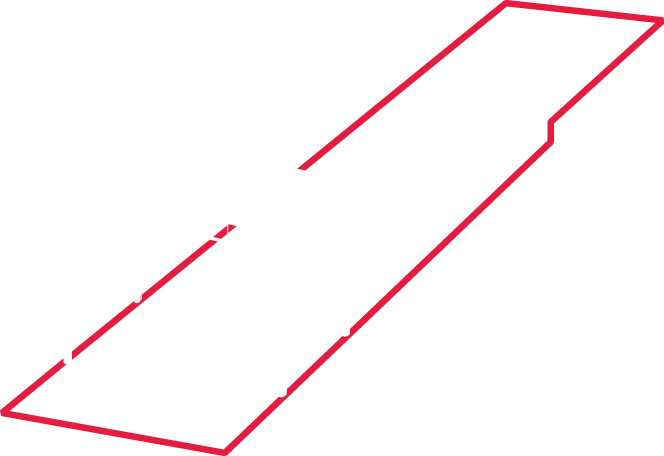
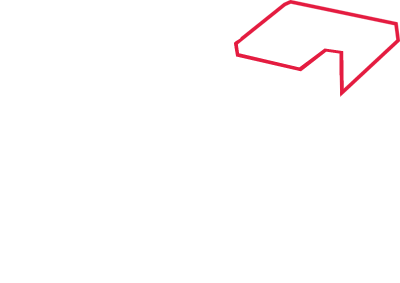
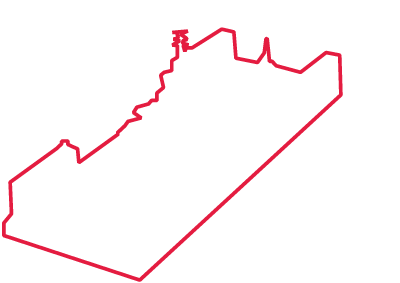
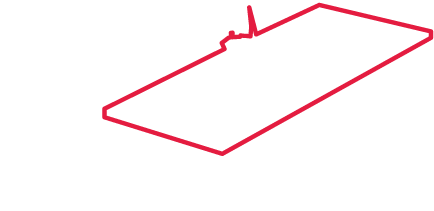
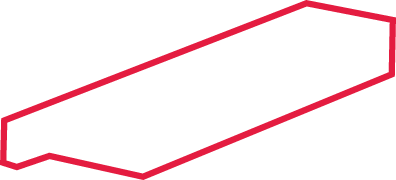
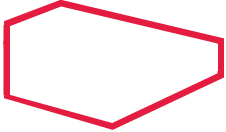
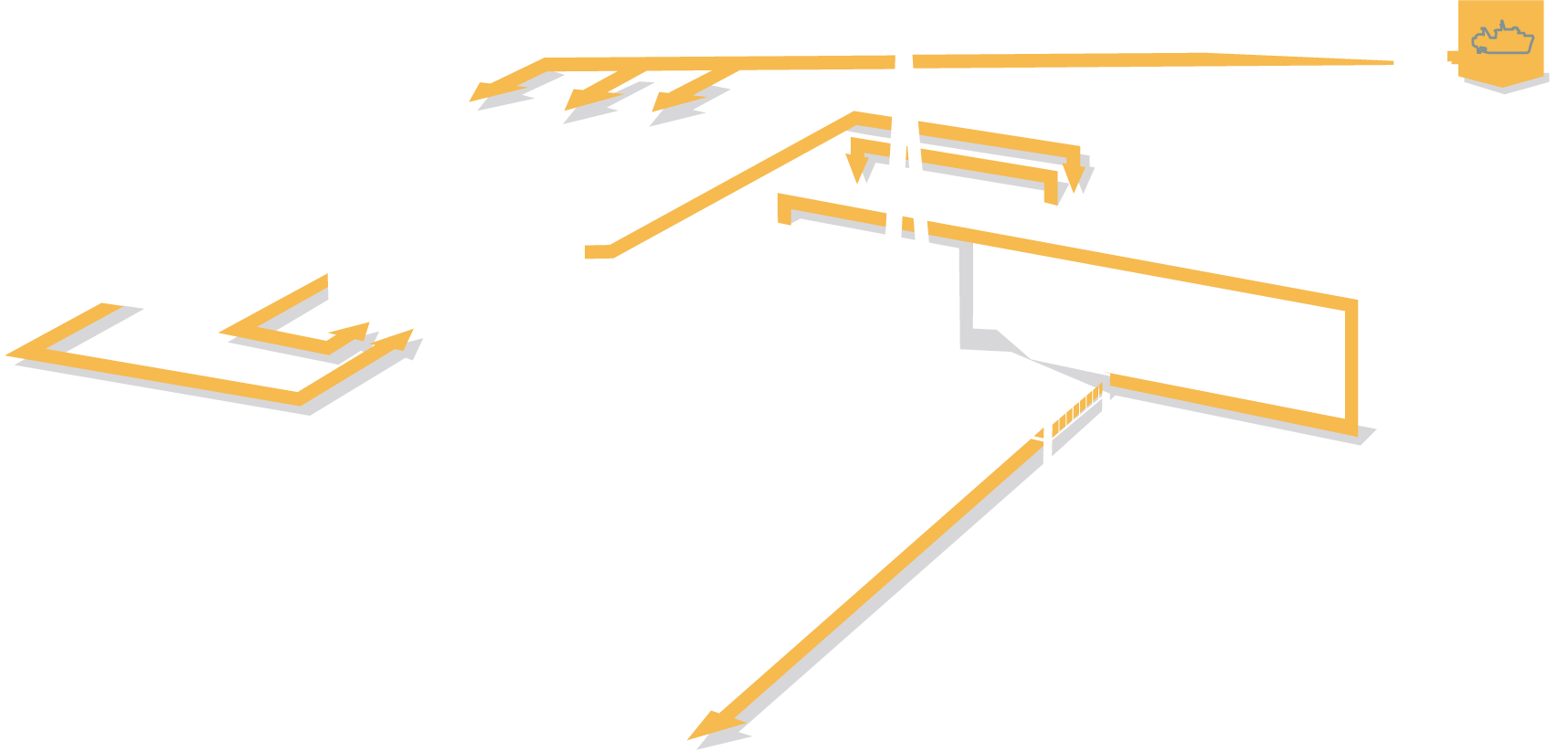
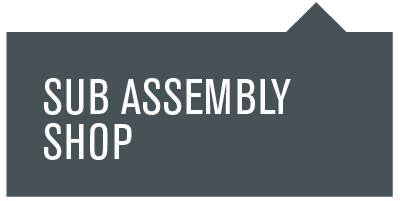
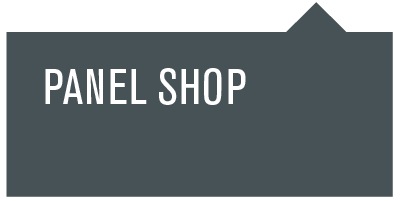
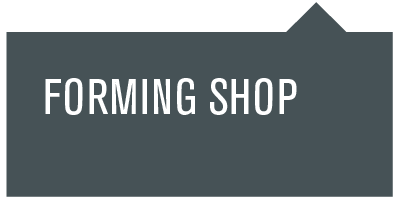
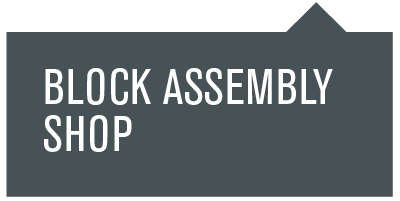
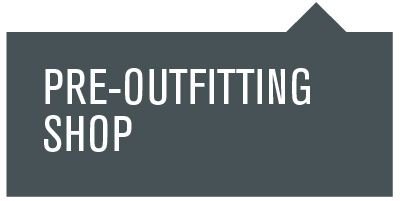
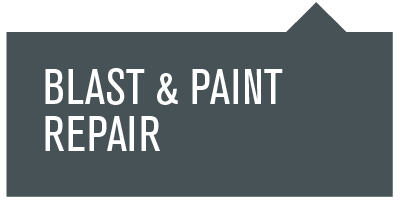
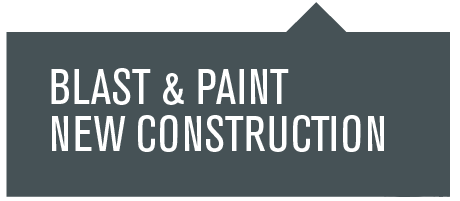
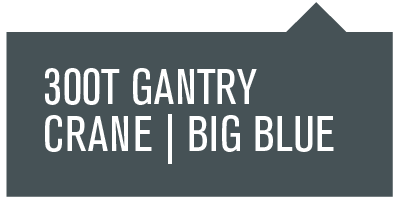
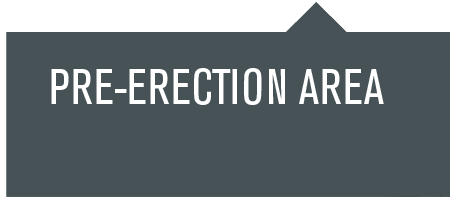
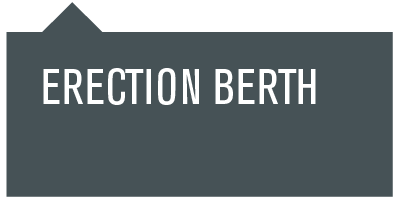
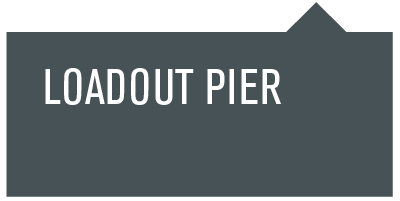
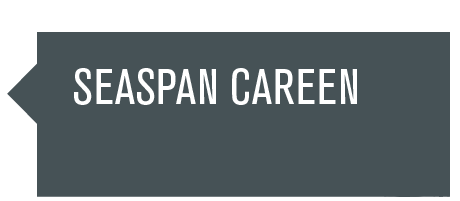
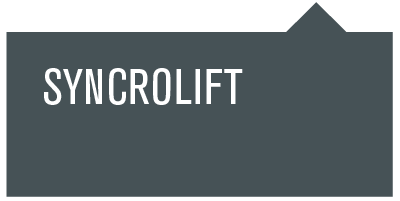
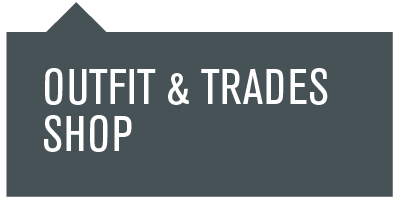
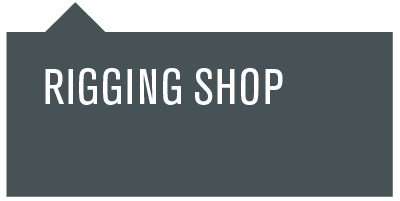

Key Features
- Computer controlled plasma cutting machine
- Computer controlled robotic profile line
- Oxy fuel cutting machine
- Five (5) bridge cranes (5T to 20T)
Dimensions
- 168m long x 24m wide
(551 ft. x 78 ft. wide) - Total size: 4000m²
(43,000 sq. ft.)
Workforce
- 30 to 40 employees per shift
- The facility operates 16 hours/day, 5 days a week
Description
The Sub Assembly Shop is the first stop in the shipbuilding process. Steel is delivered to this facility, which houses the most world-class, state-of-the-art equipment available for cutting steel plates and profiles.
In addition to a 13 meter ESAB plasma cutting/tracing/beveling/marking machine, which covers two work stations to provide for a continuous flow of work (steel can be loaded and cut on one while another is prepped), the 4000m² (43,000 sq. ft.) shop also includes a processing line equipped with a CNC robotic profile cutting machine, and five (5) stations dedicated to the assembly of small parts and sub-assemblies.

Key Features
- Panel Line (automated conveyor line to produce 12m x 12m
(39 ft. x 39 ft.) flat stiffened panels) - One-side submerged arc plate welding
- Panel cutting, layout and marking
- Stiffener fitting
- Stiffener welding
- Three stations for installation of web frames, girders, bulkheads, etc.
Dimensions
- 170m long x 28m wide
(557 ft. long x 91 ft. wide) - Total size: 4760m²
(51,236 sq. ft.)
Workforce
- 30 to 40 employees
- The shop operates 16 hours/day,
5 days/week
Description
Efficiency is the operative word for this step in the shipbuilding process. The purpose of the Panel Shop is to produce flat panels. To start the procedure, a three-headed submerged arc Welding Machine, from Lincoln Electric, joins steel plates up to 12m (39 ft.) in length. The unit welds two plates together from one side in a single pass, making the process approximately 14 times quicker than traditional methods, which also requires more manpower for tasks like turning the gigantic panels.
In addition, the Panel Line accurately cuts the perimeter of the panel and all internal holes required for installation of piping, cabling, etc. Following the steel down the conveyer line, stiffeners are automatically fit to the panel (again, with greater efficiency and accuracy) as six (6) automated welding heads working at once provide amazing efficiencies for the joining of stiffeners to the panel.
By the time the panel reaches the end of the line, it's ready to be moved using self propelled modular transporters (SPMTs) to the Block Assembly Shop.

Key Features
- 1000T plate press
- 1000T press brake
- 400T press brake
- 500T stiffener forming
- 8ft. plate rolls
Dimensions
- 130m long x 14m wide
(426 ft. long x 45 ft. wide) - Total size: 4160m²
(51,218 sq. ft.)
Workforce
- 10 to 15 employees
- The shop operates 16 hours/day,
5 days/week
Description
The Forming Shop forms/bends steel plates and profiles to the ship's final hull shape. This shop also boasts one of the most technologically advanced pieces of machinery in shipbuilding today – a 1000T Hydraulic Plate Press. The cold forming press can shape steel up to two and a half inches thick. Once the steel is formed, it moves to a section within the Block Assembly Shop that consists of steel pin jigs to allow pieces to be welded together.

Key Features
- Two 40T overhead cranes, each with two 40T trolleys
- Two 15T overhead cranes used for setting of web frames, bulkheads, etc.
- Pin jigs (adjustable telescoping pipes) for supporting curved panels during their manufacturing process
Dimensions
- 130m long x 30m wide
(426 ft. long x 98 ft. wide) - Total size: 3900m²
(42,000 sq. ft.)
Workforce
- 100 to 120 employees per shift
- The shop operates 16 hours/day,
5 days/week
Description
This is a new state of the art facility for fitting and welding of vessel hull blocks up to 24m x 24m (78 ft. x 78 ft.) in size. The Block Assembly Shop is also where curved and three-dimensional blocks are manufactured along with installation of hot outfitting items, like hangers for cables and pipes. With the joining of welded sub-assemblies and panels together, the vessel begins to take a recognizable shape in this shop. Steel panels from the panel line and sub-assemblies are brought together in 20 to 40 tonne pieces, and are assembled into hull blocks in this shop before taking one of two routes, either directly to the Pre-Outfitting Shop or more typically to the Blast & Paint Shop.

Key Features
- Block Outfitting five (5) bays to install equipment, pipe, ventilation and electrical systems with overhead cranes
- Module Construction two (2) bays for installation of outfit components onto structural frameworks
Dimensions
- 180m long x 29m wide
(590 ft. long x 95 ft. wide) - Total size: 5220m²
(56,150 sq. ft.)
Workforce
- 100 to 120 employees in the Pre-Outfitting Shop
- 100 to 150 employees in the Operations Centre (office)
- This shop operates 16 hours/day,
5 days/week
Description
This is a new dual purpose, two-floor facility. The first floor consists of five (5) bays for the outfitting of vessel hull blocks with mechanical, piping, cables, HVAC, electrical and any other system requirements, two (2) bays for the fabrication and assembly of equipment modules, and central warehousing facilities.
The second floor houses Vancouver Shipyard's Operations Centre with offices, conference rooms, training rooms, a 600-seat lunchroom and other trade amenities.

Key Features
- Environmentally controlled blast and paint facility capable of completely enclosing a wide range of small vessels and barges
- Shop used for third party ship repairs, as well as Seaspan's fleet of tugs and barges
- Can accommodate vessels up to 75m (246 ft.) in length and 22m
(72 ft.) in height
Dimensions
- 76m long x 26.2m wide
(249 ft. long x 85 ft. wide) - Total size: 2000m²
(21,500 sq. ft.)
Workforce
- 15 to 25 employees
- The shop operates 16 hours/day,
5 days/week
Description
The Repair Blast & Paint Shop was an existing facility modernized to include new cladding, ventilation, heating and blasting equipment, and a new sliding door at the south end. Both the Repair Blast & Paint Shop and the New Construction Blast & Paint Shop adhere to the highest environmental standards (they are fully ventilated and have filtration systems that capture particulate matter and other debris).

Key Features
- Two blast positions
- Steel grit vacuum and elevator recovery system
- Dedicated dust collection systems
- Four paint positions
Dimensions
- 60m long x 46m wide
(196 ft. long x 150 ft. wide) - Total size: 2760m²
(30,000 sq. ft.)
Workforce
- 25 to 50 Employees
- The shop operates 16 hours/day,
5 days/week
Description
The New Construction Blast & Paint Shop is used for steel shot blasting, surface preparation (i.e. the removal of rust and contaminants), and the painting of hull blocks, while the Repair Blast & Paint Shop was an existing facility modernized to include new cladding, ventilation and blasting equipment and a new sliding door at the south end, similar in design to an aircraft hanger. Both the New Construction Blast & Paint Shop and the Repair Blast & Paint Shop adhere to the highest environmental standards (they are fully ventilated and have filtration systems that capture particulate matter and other debris).

KEY FEATURES
- Hook height – 70m (220 ft.)
- Bridge span – 76m (249 ft.)
- Travel speed – 30m (98 ft.)
per minute - Hoist speed – 12m (39 ft.)
per minute
Dimensions
- 80m high x 76m wide
(262 ft. high x 249 ft. wide)
Workforce
- One crane operator with a 4 to 6 member ground crew
- The crane operates 16 hours/day, 5 days/week
Description
Canada's largest permanent gantry crane, with a lifting capacity of up to 300 tonnes, is used for the pre-erection and erection of blocks and grand blocks (pieces of the ship welded together to form the final product). The crane travels 250 metres (820 ft.) north and south and spans 76 metres.

Description
The pre-erection area, located on the east side of the yard and under the 300T Gantry Crane (Big Blue), is used to join hull blocks together to form grand blocks. After the blocks are joined, outfitting systems are installed across block breaks.
Rolling shelters are transferred over the blocks/grand blocks to provide sheltered workplaces.
Once grand blocks are complete and assembled as one large section, the shelters are moved to prepare the grand blocks for erection.

Description
The Erection Berth provides a flat level concrete surface where vessels up to 200 metres in length are erected. As grand blocks are completed in the Pre-Erection Area, the 300T Gantry Crane (Big Blue) lifts the grand blocks (if not exceeding 300T) onto the Erection Berth. Grand blocks forming the bottom of the vessel can reach up to 800T and are moved by Self-Propelled Mobile Transporters (SPMTs) to the erection berth.
The Erection Berth receives all grand blocks for the final assembly of the vessel. Work at this stage also includes completion of all outfitting, testing of systems, and final paint. The vessel is 95% complete before leaving the berth for its first trip to the water.

Description
The transfer of the vessel from land to sea consists of a roll-on floating platform, which is then transferred into deeper water and sunk, leaving the new vessel to float.
The floating platform is called the Seaspan Careen, an autonomous drydock with its own generators to provide power. The Loadout Pier was constructed at the end of the Erection Berth in order to tie the drydock into the yard and with sufficient water depth. The end of the Loadout Pier measures 32m (104 ft.) in width, the same as the Seaspan Careen.

Dimensions
- Length – 131m (430 ft.)
- Breadth – 48.768m (160 ft.)
- Depth to top deck – 23.165m (76 ft.)
- Depth to main deck – 7.620m (25 ft.)
- Depth to safety deck – 18.288m (60 ft.)
- Max. immersed draft (floating dock) – 19.660m (64 ft.)
- Max. draft (load line as barge) – 5.672m (18 ft.)
Main Machinery
- Generator Engine
- 3 x 550 HP x 1800 RPM
- Caterpillar 3412 A
- Purifier
- 1 x 2000 litres/hour
- Alpha – Laval
- MAB 204 S – 24 – 60 (Laval)
Description
The Seaspan Careen is an autonomous drydock with it's own generators to provide power. Its maximum lift capacity is 30,480 DWT.

Key Features
- Total size: 1742m² (18,750 sq. ft.)
- 2 lathes
- Up to 8.6m (28 ft.)
- 1 horizontal milling machine
- 2 vertical milling machines
Milling Machines
- Maintenance
- Pipefitting
- Mechanical
- Electrical
- Joiner
- Machine Shop
Description
The Outfit & Trades Shop is composed of various milling machines (both horizontal and vertical), plus small and medium lathes up to 8.6m (28 ft.) in length, press drills, a band saw, and other small equipment.
The Outfit & Trade Shop is available to support a wide variety of fabrication and machining tasks for both new construction and repair programs.